过程开发期间风险管理的主要工具PFMEA

专栏简介
PFMEA是“过程失效模式与后果分析”的英文“Process Failure Mode and Effects Analysis”的缩写。为了更好地促进AQP PFMEA软件的应用,我们将以系列文章分享运用AQP PFMEA软件有效开展PFMEA工作的理念和方法,同时系统性介绍AQP PFMEA软件的特色和具体使用方法,并指导使用者如何有效开展PFMEA工作。
链企云开发的AQP PFMEA软件是在结构分析步骤中过程流程图已经绘制完毕的基础上,基于增强型流程图当中的基本操作开展进一步的失效分析和风险分析。
■ 风险管理工具
PFMEA是一种预防性风险分析的工具,其目的是通过识别过程风险帮助优化和改进制造过程的设计开发与控制。
PFMEA的过程包括三个方面:
1. 认识和评价
哪里可能出问题?
后果会如何?
2. 采取行动
可以如何行动以防止失效?
可以如何行动以减轻后果?
3. 分析结果文件化
有必要对此进行跟踪吗?
形成知识库,经验分享库
在PFMEA中首先要做的事情就是分析产品/过程,即识别过程的功能与要求,把功能和要求识别清楚后,基于功能和要求寻找潜在的失效模式,评估潜在的失效后果,进而确定导致失效的潜在原因。
有意思的是,失效模式在这里面扮演着双重角色,它是失效后果的原因,同时也是失效原因的后果。
举个例子:
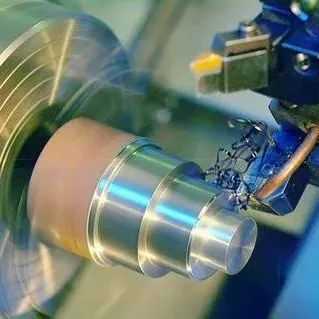
车削一根轴,轴的直径要求是20.00±0.01,若直接跳过车削,未执行车削操作,即为一种失效模式;或进行了车削,但车削后轴的直径过小或过大,这两种情形也是两种不同的失效模式。
接着,基于失效模式再通过因果关系,识别失效后果和失效原因。轴的直径过小或过大对后续装配的影响、对最终用户的影响就是失效后果;导致车削的轴直径过小或过大的原因就是失效原因,这个原因就从过程当中的人、机、料、法、环中分析寻找。
最后,针对这些失效模式、失效后果、失效原因识别已有的控制措施,如果控制措施不足,还要进一步采取措施来消除失效原因或减少失效模式发生的可能性,在生产之前暴露过程的弱点,确保在正式生产之前,这些问题都能够得到风险上的管控,提高在过程开发和制造期间探测失效模式和/或失效原因的能力,这就是PFMEA要做的事情。
值得注意的是,增强型过程流程图(PFD)是细化到基本操作层次的,所以在AQP PFMEA里是基于基本操作而不是过程步骤来分析的
■ 如何在PFMEA中评估风险
PFMEA中四大评估过程风险因素:
严重度 S
是基于某个失效模式的所有后果中最严重的后果来评价的。
发生度 O
是基于某个失效模式的某个失效原因导致该失效模式发生的可能性来评价的。
探测度 D
是基于探测措施的有效性来评价的。
通常情况下检具检查比感官检查更有效,但有时候如检查色差,直接用眼睛看比用色差仪检查更有效,但这类情形通常比较少,而且不同人的感官检查结果的一致性会比检具差。
风险优先顺序数 RPN
RPN=S×O×D,通过S、O、D的乘积来评估潜在过程问题的风险。
一般来说,分值越高,风险越高。但不可把它作为评价风险的唯一指标,更重要的是先看高严重度,再看高危害度,最后才看高RPN。
严重度高不表示发生度就高,发生度高也不表示严重度高,同样的,严重度高不表示探测度高,这三个度之间是互相完全独立的,所以可以以它们相乘的值去评价风险。
除了RPN之外,新版的AIAG-VDA FMEA和SAE FMEA里还有一个AP措施优先级。该方法首先着重于严重度S,其次为发生度O,然后为探测度D。基于S、O、D来评价针对失效模式/失效原因要采取进一步措施的优先级:H/M/L(高/中/低)。
通常来说,若AP措施优先级高就需要有相应的建议措施;若AP措施优先级低,在可行的情况下,也可以有建议措施。
风险评价核心就是通过S、O、D这几个度来衡量。
■ FMEA工业标准和指南
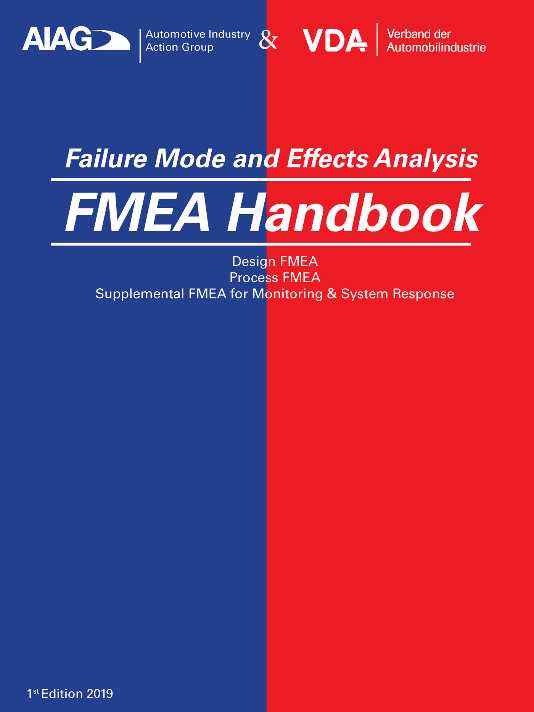

FMEA在汽车行业被列入QMS的要求,最新的FMEA标准和指南是2020年发布的AIAG-VDA FMEA手册,以及今年SAE(国际自动车工程师学会)刚出版发行的SAE FMEA标准(J1739: 2020)。
SAE PFMEA明确包含过程流程图(PFD)、PFMEA、控制计划(PMP/PCP),而且其流程图明确要求细化到微观层次的操作。
AIAG-VDA FMEA相当于是美国和德国的汽车行业协会共同制定的FMEA手册,没有强调PFMEA分析一定要细化到基本操作。
■ FMEA关注从技术方面降低风险
AQP PFMEA是团队导向的、系统性的、定性的、分析性方法,其意图是评估制造过程失效的潜在技术风险,分析这些失效的原因和后果,记录预防和探测措施,提出降低风险的建议措施。
AQP PFMEA方法关注的是技术问题,不是纪律问题。
所以在对失效模式和失效原因进行描述的时候,要用技术性的语言来描述,比如漏装螺钉、垫圈装反了,漏锁螺钉……不能简单的说操作工失误,这样才能制定出具体有效的控制措施,而不仅仅是加强培训、加强考核等纪律性管理措施。
■ AQP PFMEA过程六步法
遵循汽车行业的一般做法,将AQP PFMEA工作分成六步法。

其实也可以按AIAG-VDA FMEA手册叫七步法,第七步就是结果文件化,最终形成的AQP PFMEA的文件就是结果文件化,所以第七步在这里没有去特别强调。
PFMEA项目策划
策划是指把AQP PFMEA当成一个项目来做,前期需要确定项目的时间、节点、确定工段范围等一系列内容。
在PFMEA策划阶段,要重点关注“5T”,以便及时取得最佳效果并避免PFMEA工作返工。
PFMEA意图(inTent)
为什么要做FMEA?
PFMEA时间安排(Timing)
什么时候完成?
PFMEA团队(Team)
需要包括哪些人?
PFMEA任务(Task)
需要做哪些工作?
PFMEA工具(Tool)
如何开展分析?
准备工作是要收集与AQP PFMEA相关的文件,比如产品图纸、产品技术规范、类似制造过程的FMEA、流程图、PMP/PCP、作业指导文件等,以及类似产品在生产制造过程中和市场上的一些表现、客户投诉等信息,为后续做失效分析服务。
成功实施PFMEA项目的最重要因素之一是及时性。因此在设计开发期间 ,越早开展PFMEA越好,同时也建议公司根据特定的开发项目里程碑为他们的PFMEA定义期望的时间节点,如:
◐ 在概念阶段(确定工艺方案时)启动PFMEA项目
◐ 在充分了解生产概念时,启动PFMEA分析
◐ 在最终过程决定(即:工装模具设计和设备购买)之前,完成PFMEA分析,现实中至少在工装模具制造前完成PFMEA分析
◐ 在PPAP/PPA (即:内部PPAP批准)之前,完成PFMEA措施
预先花费时间正确地完成FMEA,产品/过程变更在早期时最容易且实施成本低廉,因而能最小化后期变更的危机。
*版权声明:本专栏所介绍的AQP PFMEA知识、软件内容及其逻辑和方法其知识产权归属江苏海岸线互联网科技有限公司和上海耕因智能科技发展中心联合所有。未经授权许可,其中的任何部分都不得被抄袭、复制或被用于软件开发之用途!
免责声明:
1、本站所有资源文章出自互联网收集整理,本站不参与制作,如果侵犯了您的合法权益,请联系本站我们会及时删除。
2、本站发布资源来源于互联网,可能存在水印或者引流等信息,请用户擦亮眼睛自行鉴别,做一个有主见和判断力的用户。
3、本站资源仅供研究、学习交流之用,若使用商业用途,请购买正版授权,否则产生的一切后果将由下载用户自行承担。
4、侵权违法和不良信息举报 举报邮箱:cnddit@qq.com
还没有评论,来说两句吧...